Читайте новини і аналітику про ритейл та e-commerce в Україні на нашій сторінці в Facebook, на нашому каналі в Telegram, а також підписуйтеся на щотижневу e-mail розсилку.
Что такое Lean и как эта методология может сократить расходы бизнеса. Кейс Modern-Expo
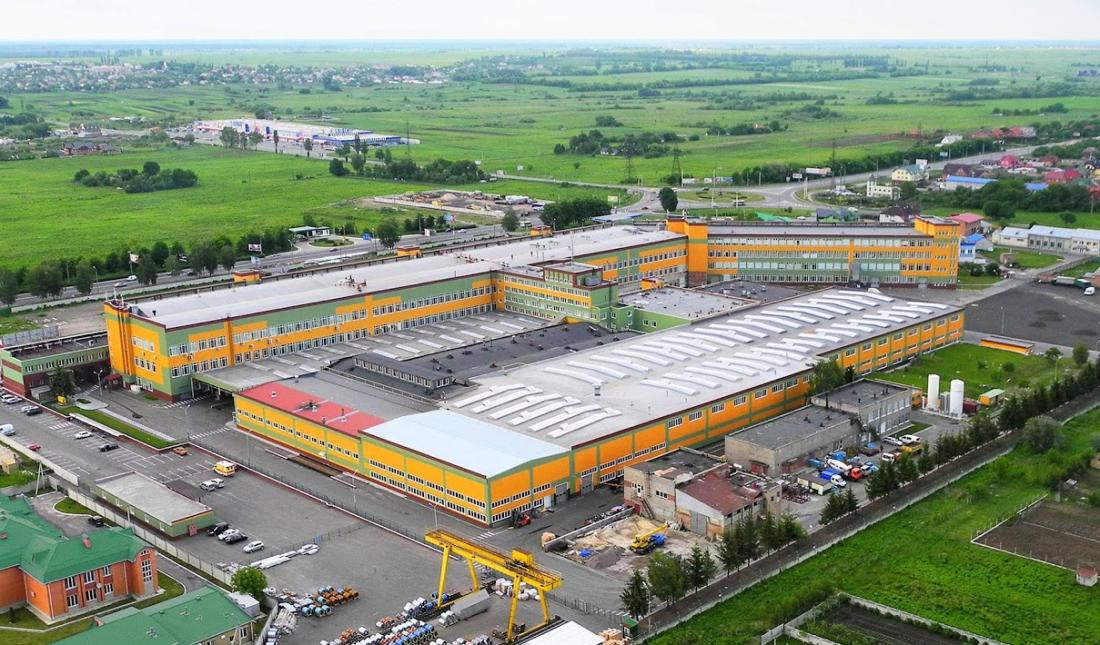
фото: пресс-служба Modern-Expo
Как с помощью технологии «бережливого производства» Lean в компании Modern-Expo сократили издержки
Когда немецкий специалист по методологии Lean посетил холдинговую компанию по изготовлению оборудования для торговли Modern-Expo, он сказал генеральному директору, что хотя компания и современная с точки зрения технологий, но организация процессов находится на уровне 1980-х годов прошлого века. На следующий день совладелец Modern-Expo Петр Пилипюк начал читать книгу «Производственная система Тойота» Таити Оно о методологии Lean, которая зародилась на автоконцернах марки Toyota. Вскоре он решил применить ее в своей компании. Он проанализировал процессы работы с главной ценностью компании — проданным оборудованием — и изменил три вещи: внедрил систему 5S, оптимизировал рабочие помещения и методы работы с заказами. Так Modern-Expo перешла на методологию Lean.
Принципы Lean: пересмотреть потери и убрать лишнее
Lean — это набор принципов для оптимизации работы предприятия. Как она помогла Toyota? С помощью Lean Toyota довела все рабочие процессы до четкой стандартизации, а все лишнее — потери на предприятии — убрала. Такой подход в японской компании назывался «бережливое производство», то есть улучшение продуктивности на всех этапах производства без высоких затрат. В Lean процессы работы сосредоточены на конечной ценности компании (проданном товаре) и удалении тех действий, которые не создают дополнительной ценности. Чтобы провести тест и определить, что важно, а что нет, поставьте вопрос: «Помогает ли это действие быстрее прийти к конечной ценности?». Результат работы с Lean — сэкономленное время, которое позволит обработать большее количество заказов.
Акцент на главной ценности помогает определить, на чем предприятие теряет свои ресурсы, и перераспределить работу так, чтобы этих потерь не было. Например, под потерями, согласно Lean, подразумевают лишние транспортировку, запасы, движения, ожидание, перепроизводство, обработку, дефекты, неиспользованный человеческий потенциал. Чтобы дополнительно упростить процессы, в Lean пересматривают использование места на полках, пополнение новыми позициями, удаление или расширение узких мест на потоке поставок.
Modern-Expo внедряли Lean на производстве в течение 6 месяцев. За это время только логистика в компании стала эффективнее на 30%.
Базовый инструмент Lean — система 5S. Систему для организации рабочего места тоже придумали в Японии. В основе названия — 5 слов на японском, которые переводятся как: сортировка (нужного и ненужного), соблюдение порядка (каждому предмету свое место), содержание в чистоте (уборка), стандартизация (поддержание порядка), совершенствование (формирование привычки). Эти привычки не только лежат в основе философии уборки, но и соответствуют принципам бережливого и малозатратного производства.
Текст на фото: Википедия
Что поменялось в Modern-Expo
После прочтения книги о Toyota Петр Пилипюк обратился со своими идеями к директору производства Игорю Мордасу. Они начали с простых, но ежедневных изменений, вовлекая в процесс все больше людей. Общение началось со средним менеджментом на производстве, с начальниками цехов, технологами. Паралелльно все начали читать специальные книги для производственного персонала и обменивались мнениями.
Руководители компании понимали, что ни один человек не будет работать по новой системе на полную, если не поймет своей выгоды. Нужно было показать, что бережливое производство приведет к снижению потерь, в том числе и денежных, соответственно, получению большей прибыли и возможности стимулировать рост зарплаты. Поэтому в компании ввели различные системы доплат за активности, которые люди применяют в экономном производстве. Работник получил задание наладить свою работу так, чтобы она стала легче, а он еще получит за нее дополнительные деньги. И это сработало. «Помню одного токаря из старшего поколения, который был категорически против методологии 5S. Но когда вокруг него начали наводить порядок, он остался единственным, кто этого не сделал. Теперь он один из самых ярых сторонников 5S, потому что получил большое моральное удовлетворение от изменений. Вывод прост: для изменений нужна мотивация. И не только материальная, но и эмоциональная», — рассказывает Петр Пилипюк.
Фото: пресс-служба Modern-Expo
Погрузившись в изучение системы Lean, сотрудники компании сразу обнаружили неправильное распределение технологий. Например, все десять лазерных комплексов для изготовления оборудования были расположены в одном цеху. Это было удобно в обслуживании, но до и от этих станков преодолевались большие расстояния. Так, шаг за шагом в компании начали оценивать потери. Например, поняли, что нужно выстроить работу таким образом, чтобы использовать как можно меньше помещений.
Также в Modern-Expo обнаружили, что определенное изделие в процессе изготовления могло «путешествовать» по предприятию многие километры. Компания проанализировала процесс и сделала так, чтобы эти продукты в одно касание проходили все необходимые процессы. И путь прохождения через завод сократился с 5 км до 300 м.
Каждый цех стал упаковывать продукт на месте, после чего он сразу отправлялся на склад, будучи уже полностью готовым к отправке клиенту. В каждому цеху сотрудники самостоятельно следят за качеством товара. Следующим шагом по изменению трансформации завода Modern-Expo стал отказ от склада готовой продукции (дополнительные потери), и компания перешла на изготовление оплаченных заказов. Это позволило сократить время хранения продукции на складе до трех дней. «Площадь складских помещений резко уменьшилась, и мы заморозили строительство дополнительного корпуса, восстанавливать которое пока не собираемся. Благодаря Lean мы увидели, что можно на меньшей площади, меньшим количеством оборудования и людей выпускать больший объем продукции, чем это было раньше», — говорит CEO компании Петр Пилипюк.
Фото: пресс-служба Modern-Expo
Постепенно в Modern-Expo начали внедрять потоки, организовывать производственные ячейки таким образом, чтобы провести там максимальное количество операций. Это и был тот момент, когда началась радикальная трансформация завода: изменился подход к распределению цехов, когда в компании отошли от технологического подхода и сосредоточились на продуктовом. С одной стороны, это усложнило уход за оборудованием, потому что сосредоточенные возле однотипных станков специалисты разъехались по разным цехам, но это резко ускорило выпуск продукции. Время производства сократилось с недели до 2 дней, компания получила большую экономию места и изменила подход к планированию.
Одной из потерь стал неиспользованный человеческий потенциал. Раньше в отделе контроля было 45 человек. Сейчас, когда цехам перешла ответственность за товар, там работает не более 10 специалистов. Товар, который появляется в цеху, уже не перепроверяют на качество второй раз, и люди нацелены на работу с серьезными проблемами, если они появятся. Таким образом, резко сократилась потребность в таких специалистах, как контроллеры, упаковщики. В результате — качественный продукт и сэкономленное время.
Автор: Валерия Дорош
Руководитель Lean Институт Украины Сергей Комберянов — спикер Modern Retail Forum, который пройдет 20 февраля в «КиевЭкспоПлаза». Во время форума он расскажет о том, как технология Lean может быть применена в ритейле. Узнать больше о мероприятии и купить билеты можно по ссылке